8. How to think about division
The following points are the elements to think about dividing the electrode about the objective machining area of EDM.
- At the time of electrode processing, is it possible to do finish machining with a same tool in all shape portions of the electrode without tool exchange?
- At the time of EDM, is the machining area in the range where objective finish surface roughness and corner R can be gained?
- At the time of EDM, is the machining area in the range where objective finish surface roughness and corner R can be gained?
When dividing an electrode, there are advantageous points and disadvantageous points, and it is necessary to judge this.
1) Advantageous points of dividing an electrode
(1) Electrode accuracy improves because of dispensing with cutting tools of small diameter in electrode processing.
As shown in Figure 1, the use of cutting tools of small diameter may not be avoided with the complicated electrode shape in electrode processing. It becomes easy to attain electrode machining accuracy by avoiding cutting tools of small diameter by the division of the electrode. In addition, you must avoid the exchange of cutting tools in the middle of finish machining because it reduces electrode machining accuracy. In electrode machining with one finish tool, it is limited to the occurrence of the relative error of shape dimensions as the whole, and it can be compensated by orbit function at the time of EDM. However, in the machining with plural finish tools, accuracy errors occur in various parts of the electrode shape, and there is no method to correct such partial errors at the time of EDM. Such use of electrodes tends to lead to defects in the finish surface roughness during EDM.
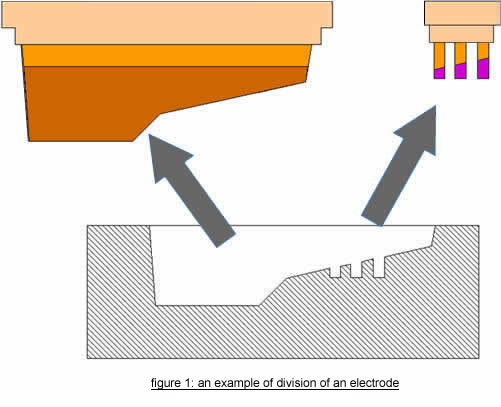
(2) Finish surface roughness can be fine.
As shown in Figure 2, in EDM, the smaller the electrode is and the smaller the machining area is, the finer finish surface roughness can be.
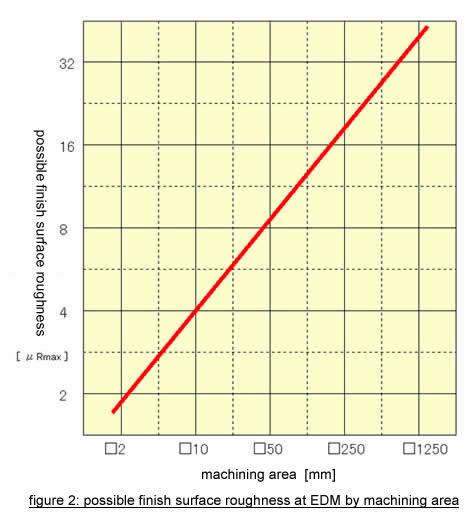
(3) A small corner R of machining area in EDM.
As shown in Figure 3, in EDM, the corners of the bottom portion can be a sharp edge because the smaller the machining area is, the less wear of electrodes for finishing area is.
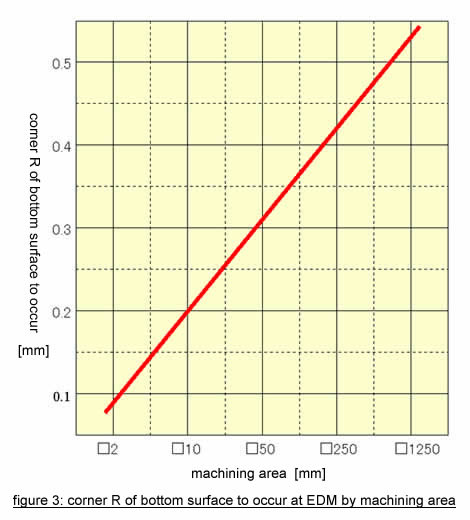
2) Disadvantageous points of dividing an electrode
(1) At EDM, it is difficult to make the dimensional accuracy same in each machining area of each electrode.
Machining accuracy tends to be different in the machining area by each electrode.
(2) It increases setup work of EDM.
Electrode number increases by dividing it, and the setup work will increase. The setup work is proportional to the number of electrodes.
(3) Rough machining speed decreases when an electrode is extremely divided.
When the machining area by each electrode becomes small by extremely dividing an electrode, it is necessary to reduce the rough machining condition, and as a whole, rough machining speed will decrease.
3) Attention to dividing an electrode
As shown in Figure 4, you must avoid dividing an electrode halfway of a continuous machining surface in a machining area as much as possible. Even if you process a continuous machining surface with different electrodes, the machining accuracy and the surface roughness tend to become uneven, and it will take time to adjust them as a result.
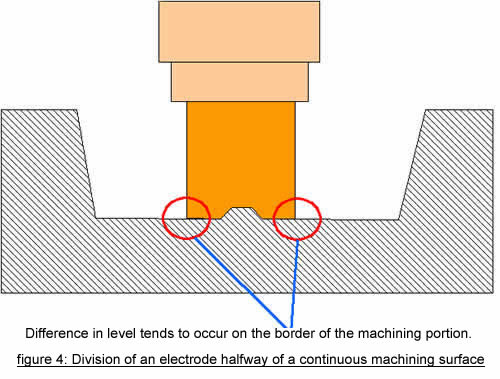